Добро пожаловать в Сообщество производственных менеджеров
![]() |
Добро пожаловать в Сообщество производственных менеджеров, промышленный форум номер один в России и СНГ. Регистрация открыта для всех, поэтому зарегистрируйтесь и принимайте участие в дискуссиях прямо сейчас! Вход Регистрация |


Кайдзен и рацпредложения: примеры из жизни
Автор: Сергей Жишкевич, Mar 14 2018 02:04 PM
кайдзен рацпредложения
520 сообщений в этой теме
#51
Отправлено 25 January 2019 - 10:53 AM
#металлургия
Уральская сталь - начальник участка высоковольтных линий электропередач ЦСП Андрей Воротников внес на Фабрику идей предложение по усилению изоляции высоковольтной линии. Андрей по опыту обслуживания линии знает, что изоляция высоковольтной линии 110 кВ – традиционный объект повышенного внимания. Провода на ней крепятся к полимерным линейным подвесным изоляторам, которые также используются в распределительных устройствах электростанций и подстанций переменного тока.
– Проблема высоковольтных неизолированных проводников – утечка тока. �? если мы установим для него дополнительную преграду, увеличив длину пути потенциальной утечки, это повысит надежность всей линии. Для этого к изолятору ЛК 70/110 я предложил добавить изолятор типа ПСД 70 Е, – поясняет автор.
Такая конструкция может применяться в условиях повышенной запыленности, причем без увеличения строительной высоты. Что позволяет применить идею при ремонтах и реконструкциях всех существующих высоковольтных линий комбината и существенно повысить надежность электроснабжения. �?дея Андрея Воротникова принята к реализации.
Уральская сталь - начальник участка высоковольтных линий электропередач ЦСП Андрей Воротников внес на Фабрику идей предложение по усилению изоляции высоковольтной линии. Андрей по опыту обслуживания линии знает, что изоляция высоковольтной линии 110 кВ – традиционный объект повышенного внимания. Провода на ней крепятся к полимерным линейным подвесным изоляторам, которые также используются в распределительных устройствах электростанций и подстанций переменного тока.
– Проблема высоковольтных неизолированных проводников – утечка тока. �? если мы установим для него дополнительную преграду, увеличив длину пути потенциальной утечки, это повысит надежность всей линии. Для этого к изолятору ЛК 70/110 я предложил добавить изолятор типа ПСД 70 Е, – поясняет автор.
Такая конструкция может применяться в условиях повышенной запыленности, причем без увеличения строительной высоты. Что позволяет применить идею при ремонтах и реконструкциях всех существующих высоковольтных линий комбината и существенно повысить надежность электроснабжения. �?дея Андрея Воротникова принята к реализации.
#52
Отправлено 01 February 2019 - 03:32 PM
ТРАТ�?М 1 ЧАС ВМЕСТО 5-ти
С апреля 2017 года в состав Лениногорского теплоэнергетического цеха ООО «Тепло-ЭнергоСервис» вошла бригада по ремонту теплоэнергетического оборудования в количестве 4 человек. Основная задача бригады - выполнение ремонта котельного оборудования и тепловых сетей как собственного, так и сторонних заказчиков.
Специалисты занимаются тепловой изоляцией трубопроводов, емкостей и запорной арматуры. Чтобы качественно утеплить трубопровод тепловой сети, необходимо обернуть его теплоизоляционным материалом, который, в свою очередь, покрывается полиэтиленовой пленкой и оцинкованным листом. В процессе проведения работ требуется предварительно изготовить заготовки из оцинкованной стали.
Этот этап является довольно трудоемким и отвлекает на себя ресурсы практически всей бригады, то есть на данном этапе задействовано 2 слесаря-ремонтника. К тому же занимает большое количество рабочего времени, к примеру, для изготовления 30 заготовок затрачивается 7 часов.
В поисках решения этой проблемы заместитель начальника ЛТЭЦ Ринат Газизуллин и автор этих строк, мастер бригады Сергей Куличков, провели анализ всех этапов изготовления заготовок посредством составления карты текущего состояния процесса. За расчет взяли процесс изготовления 30 деталей.
Первый и второй этапы включают в себя получение задания, прохождение целевого инструктажа и разлиновку листа оцинкованной стали, что занимает в общей сложности 45 минут. Третий этап представляет собой резку разлинованного по размерам листа ножницами по металлу и по времени составляет 75 минут. Четвертый, заключительный, этап – гибка заготовок вручную по окружности требуемого диаметра, занимающая 300 минут. Таким образом, весь процесс составляет 420 минут.
Я предложил механизировать третий и четвертый этапы. Руководство цеха приняло решение о механизации производственного процесса за счет применения загибочного станка и электроножниц. Механизация данного процесса позволило сократить затрачиваемое время на резку металла с 75 до 15 минут, а на гибку заготовок – с 300 до 60 минут. Применение данного процесса позволило увеличить производительность на 71 % и сократить общее время процесса до 120 минут. Кроме того, внедрение нового оборудования привело к улучшению условий труда посредством механизации рабочего процесса.
С апреля 2017 года в состав Лениногорского теплоэнергетического цеха ООО «Тепло-ЭнергоСервис» вошла бригада по ремонту теплоэнергетического оборудования в количестве 4 человек. Основная задача бригады - выполнение ремонта котельного оборудования и тепловых сетей как собственного, так и сторонних заказчиков.
Специалисты занимаются тепловой изоляцией трубопроводов, емкостей и запорной арматуры. Чтобы качественно утеплить трубопровод тепловой сети, необходимо обернуть его теплоизоляционным материалом, который, в свою очередь, покрывается полиэтиленовой пленкой и оцинкованным листом. В процессе проведения работ требуется предварительно изготовить заготовки из оцинкованной стали.
Этот этап является довольно трудоемким и отвлекает на себя ресурсы практически всей бригады, то есть на данном этапе задействовано 2 слесаря-ремонтника. К тому же занимает большое количество рабочего времени, к примеру, для изготовления 30 заготовок затрачивается 7 часов.
В поисках решения этой проблемы заместитель начальника ЛТЭЦ Ринат Газизуллин и автор этих строк, мастер бригады Сергей Куличков, провели анализ всех этапов изготовления заготовок посредством составления карты текущего состояния процесса. За расчет взяли процесс изготовления 30 деталей.
Первый и второй этапы включают в себя получение задания, прохождение целевого инструктажа и разлиновку листа оцинкованной стали, что занимает в общей сложности 45 минут. Третий этап представляет собой резку разлинованного по размерам листа ножницами по металлу и по времени составляет 75 минут. Четвертый, заключительный, этап – гибка заготовок вручную по окружности требуемого диаметра, занимающая 300 минут. Таким образом, весь процесс составляет 420 минут.
Я предложил механизировать третий и четвертый этапы. Руководство цеха приняло решение о механизации производственного процесса за счет применения загибочного станка и электроножниц. Механизация данного процесса позволило сократить затрачиваемое время на резку металла с 75 до 15 минут, а на гибку заготовок – с 300 до 60 минут. Применение данного процесса позволило увеличить производительность на 71 % и сократить общее время процесса до 120 минут. Кроме того, внедрение нового оборудования привело к улучшению условий труда посредством механизации рабочего процесса.
#53
Отправлено 01 February 2019 - 03:41 PM
#машиностроение
На участке гуммировки производства общей техники ЗиО-Подольска внедрено средство малой механизации – роликовый конвейер.
Многие годы гуммировщики устанавливали формы в пресс вручную. Для самых тяжелых, массой 100–150 кг, использовали незамысловатые приспособления – на металлический стол устанавливали трубки и по ним передвигали пресс-формы. «�?ной раз они у нас падали, благо молодые были, шустрые, успевали отбегать. Доставали из пресса, взявшись за ручки, на счет раз-два. Физически тяжело было», – рассказывает гуммировщик с более чем 40-летним стажем Геннадий Шукалев.
Сейчас ситуация изменилась. В рамках повсеместного внедрения инструментов ПСР рабочие предложили внедрить рольганг – роликовый конвейер (транспортер). Это предложение по улучшениям (ППУ) поддержали специалисты по развитию ПСР и оказали содействие в его реализации.
«За основу была взята давно разработанная конструкция, которая используется на многих участках завода, – поясняет ведущий инженер-конструктор отдела нестандартного оборудования Сергей Гаврилов. – Основная конструкторская задача, которая была поставлена перед нами, – вписать рольганг в определенные производственные условия. По нашим чертежам конвейер изготовили в инструментальном цехе. Данное средство малой механизации оправдало себя. Оно принесло существенную пользу: облегчило труд людей, снизило уровень травмоопасности. Без особых усилий вынуть пресс-форму позволяет установленная лебедка с ручным приводом. Теперь мы прилагаем минимальные физические усилия при гуммировании деталей. Легче стало, а главное, безопаснее, и скорость установки пресс-формы увеличилась в два раза».
На участке гуммировки производства общей техники ЗиО-Подольска внедрено средство малой механизации – роликовый конвейер.
Многие годы гуммировщики устанавливали формы в пресс вручную. Для самых тяжелых, массой 100–150 кг, использовали незамысловатые приспособления – на металлический стол устанавливали трубки и по ним передвигали пресс-формы. «�?ной раз они у нас падали, благо молодые были, шустрые, успевали отбегать. Доставали из пресса, взявшись за ручки, на счет раз-два. Физически тяжело было», – рассказывает гуммировщик с более чем 40-летним стажем Геннадий Шукалев.
Сейчас ситуация изменилась. В рамках повсеместного внедрения инструментов ПСР рабочие предложили внедрить рольганг – роликовый конвейер (транспортер). Это предложение по улучшениям (ППУ) поддержали специалисты по развитию ПСР и оказали содействие в его реализации.
«За основу была взята давно разработанная конструкция, которая используется на многих участках завода, – поясняет ведущий инженер-конструктор отдела нестандартного оборудования Сергей Гаврилов. – Основная конструкторская задача, которая была поставлена перед нами, – вписать рольганг в определенные производственные условия. По нашим чертежам конвейер изготовили в инструментальном цехе. Данное средство малой механизации оправдало себя. Оно принесло существенную пользу: облегчило труд людей, снизило уровень травмоопасности. Без особых усилий вынуть пресс-форму позволяет установленная лебедка с ручным приводом. Теперь мы прилагаем минимальные физические усилия при гуммировании деталей. Легче стало, а главное, безопаснее, и скорость установки пресс-формы увеличилась в два раза».
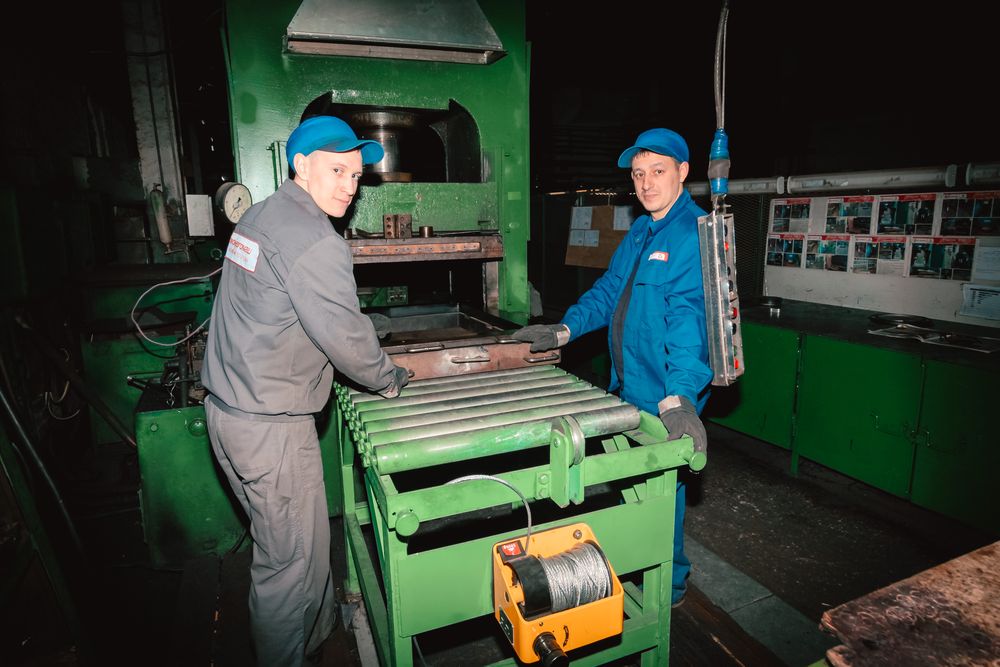
#54
Отправлено 05 February 2019 - 03:50 PM
да уж
каменный век
каменный век

#55
Отправлено 15 February 2019 - 11:26 AM
#энергетика
Более 690 тысяч рублей составил экономический эффект от реализации новаторской идеи ведущего инженера-технолога турбинного цеха Сергея �?зотова. Она заняла второе место в конкурсе среди работников Смоленской АЭС на лучшее предложение по улучшению.
Предложение направлено на повышение надежности работы системы маслоснабжения турбины.
– Моя идея заключалась в том, чтобы снизить рабочее давление масла на входе в маслоохладители турбины с 6 кгс/см2 до разрешенных 4 кгс/см2. Для решения этой задачи предложил уменьшить диаметр рабочего колеса насоса смазки подшипников турбины, – рассказывает он. – Помощь в реализации предложения по улучшению была оказана на всех должностных уровнях турбинного цеха, ведь чтоб воплотить идею в реальность, недостаточно ее только придумать, необходимо еще и правильно воплотить.
В результате реализации этой инженерной задумки удалось не только снизить давление масла на напоре масляного насоса турбины, а также предотвратить повышенный износ запорной арматуры, обеспечить безопасный режим эксплуатации маслоохладителя путем исключения возможности нарушения герметичности трубного пучка и выхода масла в окружающую среду. За счет всего этого уменьшилось количество внеплановых ремонтов маслоохладителей турбины и, в целом, повысилась безопасность работы оборудования.
Более 690 тысяч рублей составил экономический эффект от реализации новаторской идеи ведущего инженера-технолога турбинного цеха Сергея �?зотова. Она заняла второе место в конкурсе среди работников Смоленской АЭС на лучшее предложение по улучшению.
Предложение направлено на повышение надежности работы системы маслоснабжения турбины.
– Моя идея заключалась в том, чтобы снизить рабочее давление масла на входе в маслоохладители турбины с 6 кгс/см2 до разрешенных 4 кгс/см2. Для решения этой задачи предложил уменьшить диаметр рабочего колеса насоса смазки подшипников турбины, – рассказывает он. – Помощь в реализации предложения по улучшению была оказана на всех должностных уровнях турбинного цеха, ведь чтоб воплотить идею в реальность, недостаточно ее только придумать, необходимо еще и правильно воплотить.
В результате реализации этой инженерной задумки удалось не только снизить давление масла на напоре масляного насоса турбины, а также предотвратить повышенный износ запорной арматуры, обеспечить безопасный режим эксплуатации маслоохладителя путем исключения возможности нарушения герметичности трубного пучка и выхода масла в окружающую среду. За счет всего этого уменьшилось количество внеплановых ремонтов маслоохладителей турбины и, в целом, повысилась безопасность работы оборудования.
#56
Отправлено 21 February 2019 - 04:46 PM
#металлургия
Специалисты электросталеплавильного цеха (ЭСПЦ) сортового завода в Балакове внедрили отслеживание температуры брони сталеразливочного ковша в online-режиме.
Раньше состояние футеровки шлакового пояса стальковша оценивали визуально. Ошибка могла привести к прорыву металла сквозь ковш и повреждению оборудования. Чтобы более точно диагностировать состояние брони, мастер ЭСПЦ Павел Петров предложил использовать стационарный тепловизор. Этот прибор позволяет регулярно отслеживать температуру наиболее уязвимой части стальковша – шлакового пояса.
�?нформация с тепловизора поступает на монитор центрального пульта управления установки внепечной обработки стали. Повышение температуры до 400 градусов свидетельствует об износе футеровки. В таком случае устройство подает сигнал – и металл переливают в другой ковш для продолжения обработки стали.
Подобными устройствами также планируют оснастить броню горячей зоны рабочего пространства шахтной печи.
Специалисты электросталеплавильного цеха (ЭСПЦ) сортового завода в Балакове внедрили отслеживание температуры брони сталеразливочного ковша в online-режиме.
Раньше состояние футеровки шлакового пояса стальковша оценивали визуально. Ошибка могла привести к прорыву металла сквозь ковш и повреждению оборудования. Чтобы более точно диагностировать состояние брони, мастер ЭСПЦ Павел Петров предложил использовать стационарный тепловизор. Этот прибор позволяет регулярно отслеживать температуру наиболее уязвимой части стальковша – шлакового пояса.
�?нформация с тепловизора поступает на монитор центрального пульта управления установки внепечной обработки стали. Повышение температуры до 400 градусов свидетельствует об износе футеровки. В таком случае устройство подает сигнал – и металл переливают в другой ковш для продолжения обработки стали.
Подобными устройствами также планируют оснастить броню горячей зоны рабочего пространства шахтной печи.
#57
Отправлено 05 April 2019 - 10:46 AM
Если мероприятие содержит организационные идеи, направленные на рациональную расстановку оборудования, а главное, его реализация приведет к снижению рисков по охране труда и промышленной безопасности, то его причислят к группе «А», и заслуги автора такой идеи обязательно будут оценены. Так было отмечено предложение мастера ЦРМО Уральской Стали Сергея Зоткина, который усовершенствовал не процесс, а процедуру.
На ремонтных площадках при использовании электроинструмента часто приходится пользоваться удлинителем. Однако согласно требованиям ОТиПБ электрокабель не должен находиться на полу под ногами, чтобы избежать случайного повреждения электрооборудования и поражения сотрудника током. Да и споткнуться о провод немудрено.
Автор предложил изготовить переносные стойки, которые легко устанавливаются в необходимом месте. Они удерживают кабель в двух метрах над уровнем пола, практически исключая для работника возможность несанкционированного прямого контакта.
На ремонтных площадках при использовании электроинструмента часто приходится пользоваться удлинителем. Однако согласно требованиям ОТиПБ электрокабель не должен находиться на полу под ногами, чтобы избежать случайного повреждения электрооборудования и поражения сотрудника током. Да и споткнуться о провод немудрено.
Автор предложил изготовить переносные стойки, которые легко устанавливаются в необходимом месте. Они удерживают кабель в двух метрах над уровнем пола, практически исключая для работника возможность несанкционированного прямого контакта.
#58
Отправлено 05 April 2019 - 10:50 AM
Эта идея уже реализована, автор получил свое вознаграждение.
В производственном корпусе три ряда светильников искусственного освещения. Первый ряд находится у стены с окнами. Уровень естественного освещения производственного корпуса цеха в течение рабочей смены меняется. Утром, вечером и в пасмурную погоду включены все светильники. Но днем в солнечную погоду можно экономить, если поставить фотореле. Днем светло и хватает естественного освещения у окна на первом ряде искусственного освещения, где мы установили фотореле, выполняющее функцию автоматического отключения света. Таким образом, экономится электроэнергия и увеличивается срок службы ламп.
В производственном корпусе три ряда светильников искусственного освещения. Первый ряд находится у стены с окнами. Уровень естественного освещения производственного корпуса цеха в течение рабочей смены меняется. Утром, вечером и в пасмурную погоду включены все светильники. Но днем в солнечную погоду можно экономить, если поставить фотореле. Днем светло и хватает естественного освещения у окна на первом ряде искусственного освещения, где мы установили фотореле, выполняющее функцию автоматического отключения света. Таким образом, экономится электроэнергия и увеличивается срок службы ламп.
#59
Отправлено 05 April 2019 - 11:13 AM
Ниже - альтернативный вариант ремонта питательных насосов. Он включен в копилку лучших инициатив концерна «Росэнергоатома», повысивших эффективность работы оборудования.
Когда вывели в ремонт питательный насос, стало понятно, что резьбовая часть вала за длительный период (порядка 10 лет) износилась и больше непригодна для крепления специальной гайки. Каков традиционный выход из сложившейся ситуации? Заменить вал, но это не так просто. Во-первых, изготовитель работает на территории Украины, и поставка может затянуться на год, что недопустимо: долгий простой насоса может привести к снижению нагрузки энергоблока. Во-вторых, цена вала – около 1 млн рублей, а если учесть транспортные расходы, то и все 1,5.
Спасительная идея, как устранить дефект быстрее и дешевле, пришла в голову заместителя начальника цеха Валерия Куприна, который связан с эксплуатацией и ремонтом на Смоленской АЭС более 40 лет. Вместе с Юрием Осиповым они доработали предложение по улучшению и запустили в реализацию.
– Питательные насосы – один из важнейших элементов тепловой схемы станции, который обеспечивает надежность работы и бесперебойность отпуска электроэнергии, – рассказывает Валерий Куприн. – Они предназначены для непрерывного восполнения химически очищенной воды в парогенераторе. Это оборудование производится из специального материала по специальной технологии, чтобы без проблем перекачивать жидкость 160-градусной температуры под давлением – до 100 кгс/см2. Было решено не менять вал, а поступить иначе: резьбу проточить до средней части, изготовить втулку и установить ее «на горячую» вместо гайки. Завод-изготовитель согласовал нам такое решение.
В результате сэкономили только на закупке и поставке 1,5 миллиона, сократили сроки по поставке вала насоса. Финансовые затраты на изготовление втулки – 8 тысяч рублей, а временные – 2 дня. Главное, что предотвратили риск снижения нагрузки энергоблока, а значит, недовыработки электроэнергии.
Когда вывели в ремонт питательный насос, стало понятно, что резьбовая часть вала за длительный период (порядка 10 лет) износилась и больше непригодна для крепления специальной гайки. Каков традиционный выход из сложившейся ситуации? Заменить вал, но это не так просто. Во-первых, изготовитель работает на территории Украины, и поставка может затянуться на год, что недопустимо: долгий простой насоса может привести к снижению нагрузки энергоблока. Во-вторых, цена вала – около 1 млн рублей, а если учесть транспортные расходы, то и все 1,5.
Спасительная идея, как устранить дефект быстрее и дешевле, пришла в голову заместителя начальника цеха Валерия Куприна, который связан с эксплуатацией и ремонтом на Смоленской АЭС более 40 лет. Вместе с Юрием Осиповым они доработали предложение по улучшению и запустили в реализацию.
– Питательные насосы – один из важнейших элементов тепловой схемы станции, который обеспечивает надежность работы и бесперебойность отпуска электроэнергии, – рассказывает Валерий Куприн. – Они предназначены для непрерывного восполнения химически очищенной воды в парогенераторе. Это оборудование производится из специального материала по специальной технологии, чтобы без проблем перекачивать жидкость 160-градусной температуры под давлением – до 100 кгс/см2. Было решено не менять вал, а поступить иначе: резьбу проточить до средней части, изготовить втулку и установить ее «на горячую» вместо гайки. Завод-изготовитель согласовал нам такое решение.
В результате сэкономили только на закупке и поставке 1,5 миллиона, сократили сроки по поставке вала насоса. Финансовые затраты на изготовление втулки – 8 тысяч рублей, а временные – 2 дня. Главное, что предотвратили риск снижения нагрузки энергоблока, а значит, недовыработки электроэнергии.
#60
Отправлено 06 May 2019 - 11:24 AM
#металлургия
На БАЗе экономический эффект от простого решения устроить фильтру «химчистку» составил 622 тысячи рублей.
Кайзен-предложение увеличило срок службы металлического фильтра грубой очистки воды, который используется на установке высокого давления «Хаммельманн HDP-803». Вследствие постоянной эксплуатации ячейки фильтра регулярно зарастали твердым осадком, что снижало пропускную способность фильтра. Механическим способом такой осадок удалить не представлялось возможным. Поэтому работникам участка постоянно приходилось менять фильтр целиком. Начальник участка чистки технологического оборудования Александр Киселев и мастер участка Дмитрий Швецов решили производить химическую чистку фильтра, поместив его в специальную емкость с соляной кислотой. Фильтр стал как новенький.
Виктор Черепенин, директор ДГП БАЗа: "Кайзен значим не только для участка чистки технологического оборудования, но и для дирекции глиноземного производства в целом. Помимо значительной экономии химчистка фильтра грубой очистки воды позволила нам полностью исключить его замену".
На БАЗе экономический эффект от простого решения устроить фильтру «химчистку» составил 622 тысячи рублей.
Кайзен-предложение увеличило срок службы металлического фильтра грубой очистки воды, который используется на установке высокого давления «Хаммельманн HDP-803». Вследствие постоянной эксплуатации ячейки фильтра регулярно зарастали твердым осадком, что снижало пропускную способность фильтра. Механическим способом такой осадок удалить не представлялось возможным. Поэтому работникам участка постоянно приходилось менять фильтр целиком. Начальник участка чистки технологического оборудования Александр Киселев и мастер участка Дмитрий Швецов решили производить химическую чистку фильтра, поместив его в специальную емкость с соляной кислотой. Фильтр стал как новенький.
Виктор Черепенин, директор ДГП БАЗа: "Кайзен значим не только для участка чистки технологического оборудования, но и для дирекции глиноземного производства в целом. Помимо значительной экономии химчистка фильтра грубой очистки воды позволила нам полностью исключить его замену".
5 человек читают эту тему
0 пользователей, 5 гостей, 0 скрытых пользователей