Добро пожаловать в Сообщество производственных менеджеров
![]() |
Добро пожаловать в Сообщество производственных менеджеров, промышленный форум номер один в России и СНГ. Регистрация открыта для всех, поэтому зарегистрируйтесь и принимайте участие в дискуссиях прямо сейчас! Вход Регистрация |


Кайдзен и рацпредложения: примеры из жизни
Автор: Сергей Жишкевич, Mar 14 2018 02:04 PM
кайдзен рацпредложения
527 сообщений в этой теме
#111
Отправлено 31 March 2020 - 01:16 PM
В управлении по производству запасных частей Оскольского электрометаллургического комбината были значительно снижены затраты на электроэнергию.
Произошло это за счет замены многопостовых сварочных выпрямителей (ВДМ) на инверторные сварочные аппараты – всего 12 штук. Ожидаемый экономический эффект по году составит ориентировочно 1 миллион рублей.
?дея была воплощена быстро – за полтора месяца.Ее авторы и реализаторы также разработали карту пошагового выполнения операций, которая поможет персоналу быстро освоить новое оборудование.
Произошло это за счет замены многопостовых сварочных выпрямителей (ВДМ) на инверторные сварочные аппараты – всего 12 штук. Ожидаемый экономический эффект по году составит ориентировочно 1 миллион рублей.
?дея была воплощена быстро – за полтора месяца.Ее авторы и реализаторы также разработали карту пошагового выполнения операций, которая поможет персоналу быстро освоить новое оборудование.
#112
Отправлено 03 April 2020 - 10:49 AM
Лебединский ГОК, проект «Оптимизация затрат по укрытию кабельной эстакады для защиты от повреждений КЛ 6 кВ при проведении массовых взрывов в карьере».
В период проведения массовых взрывов с ноября 2019 по март этого года треть кабельной эстакады, которая питает передвижную подстанцию РП-11, была подвержена попаданию разлетающихся осколков горной массы. Это могло привести к повреждению кабельной линии, что повлекло бы за собой необходимость восстановления и, соответственно, сбоям энергообеспечения карьера, поэтому необходимо было произвести укрытие незащищённого участка. Обсуждалось несколько вариантов: предложенный проектно-конструкторским центром предусматривал применение большого количества тяжёлых металлоконструкций и длительное время производства работ, а оставалось чуть более двух недель до очередного взрыва!
Автор идеи предложил переложить кабели на нижнюю полку и смонтировать укрытие: «одеть» кабельную эстакаду картой из укладочной сетки, поверх которой положить бывшую в употреблении конвейерную ленту. Что и было сделано.
Важно отметить, что такая мера позволила снизить организационные и технологические простои оборудования после проведения взрывных работ — из 1 300 метров «объекта» под крышу попали более 700 метров — и принесло эффект в размере 970 тысяч рублей.
В период проведения массовых взрывов с ноября 2019 по март этого года треть кабельной эстакады, которая питает передвижную подстанцию РП-11, была подвержена попаданию разлетающихся осколков горной массы. Это могло привести к повреждению кабельной линии, что повлекло бы за собой необходимость восстановления и, соответственно, сбоям энергообеспечения карьера, поэтому необходимо было произвести укрытие незащищённого участка. Обсуждалось несколько вариантов: предложенный проектно-конструкторским центром предусматривал применение большого количества тяжёлых металлоконструкций и длительное время производства работ, а оставалось чуть более двух недель до очередного взрыва!
Автор идеи предложил переложить кабели на нижнюю полку и смонтировать укрытие: «одеть» кабельную эстакаду картой из укладочной сетки, поверх которой положить бывшую в употреблении конвейерную ленту. Что и было сделано.
Важно отметить, что такая мера позволила снизить организационные и технологические простои оборудования после проведения взрывных работ — из 1 300 метров «объекта» под крышу попали более 700 метров — и принесло эффект в размере 970 тысяч рублей.
#113
Отправлено 06 April 2020 - 11:33 AM
Как облегчить работа приёмосдатчика и сделать ее более безопасной
Для приёмосдатчиков отдела перевозок железнодорожного транспорта логистического центра на прессово-рамном заводе КАМАЗа установили камеры видеонаблюдения. Теперь за процессом погрузки можно наблюдать со своего рабочего места. В пакетировочном отделении ПРЗ погрузка металлотходов ведётся круглосуточно. Для контроля равномерности погрузки вагона приёмосдатчик должен несколько раз лично заглянуть внутрь огромной железной тары, а затем при необходимости отдать распоряжение мастеру ЦТСР для сдвига подвижного состава с помощью лебедки. Раньше для этого работникам приходилось подниматься по лесенке вагона в любую погоду, а ступени после дождя или заморозков становятся скользкими. Ночью это делать ещё сложнее, поскольку как раз по пути к вагону есть опасная зона погрузки металла.
– Установка камер видеонаблюдения избавила приёмосдатчиков от ненужного риска. Благодаря освещению уровень загрузки вагона хорошо видно ночью, к тому же теперь работникам проще распланировать своё рабочее время, ведь они также должны контролировать разгрузку и погрузку в производственном корпусе ПРЗ и на других объектах «ПЖДТ-Сервис», – пояснил начальник отдела организации перевозок железнодорожным транспортом департамента транспортной логистики ЛЦ Евгений Наборщиков.
В логистическом центе намерены сделать более безопасными и другие зоны наблюдения. В планах установка видеокамер на 8-м и 10-м пути пакетировочного отделения ПРЗ и организация видеонаблюдения в корпусе кузнечного завода, а также на станции «Литейная».
Для приёмосдатчиков отдела перевозок железнодорожного транспорта логистического центра на прессово-рамном заводе КАМАЗа установили камеры видеонаблюдения. Теперь за процессом погрузки можно наблюдать со своего рабочего места. В пакетировочном отделении ПРЗ погрузка металлотходов ведётся круглосуточно. Для контроля равномерности погрузки вагона приёмосдатчик должен несколько раз лично заглянуть внутрь огромной железной тары, а затем при необходимости отдать распоряжение мастеру ЦТСР для сдвига подвижного состава с помощью лебедки. Раньше для этого работникам приходилось подниматься по лесенке вагона в любую погоду, а ступени после дождя или заморозков становятся скользкими. Ночью это делать ещё сложнее, поскольку как раз по пути к вагону есть опасная зона погрузки металла.
– Установка камер видеонаблюдения избавила приёмосдатчиков от ненужного риска. Благодаря освещению уровень загрузки вагона хорошо видно ночью, к тому же теперь работникам проще распланировать своё рабочее время, ведь они также должны контролировать разгрузку и погрузку в производственном корпусе ПРЗ и на других объектах «ПЖДТ-Сервис», – пояснил начальник отдела организации перевозок железнодорожным транспортом департамента транспортной логистики ЛЦ Евгений Наборщиков.
В логистическом центе намерены сделать более безопасными и другие зоны наблюдения. В планах установка видеокамер на 8-м и 10-м пути пакетировочного отделения ПРЗ и организация видеонаблюдения в корпусе кузнечного завода, а также на станции «Литейная».

#114
Отправлено 10 April 2020 - 10:00 AM
Это предложение из номинации «Самый бережливый кайдзен» конкурса кайдзен-предложений филиала ПАО «Компания «Сухой» «КнААЗ им. Ю.А. Гагарина».
Проблема: при работе на крыле, с агрегатами необходимо постоянно использовать охлаждающую жидкость, в частности керосин. Есть большая вероятность, что неустойчивая тара может упасть, СОЖ и ЛКП разольются.
Решение: появилась идея — зафиксировать емкость. На глаза попался магнит, попробовал изготовить тару с магнитом — получилось. Тара с магнитной фиксацией надежно закреплена.
Проблема: при работе на крыле, с агрегатами необходимо постоянно использовать охлаждающую жидкость, в частности керосин. Есть большая вероятность, что неустойчивая тара может упасть, СОЖ и ЛКП разольются.
Решение: появилась идея — зафиксировать емкость. На глаза попался магнит, попробовал изготовить тару с магнитом — получилось. Тара с магнитной фиксацией надежно закреплена.
#115
Отправлено 23 April 2020 - 11:39 AM
АЛРОСА
Юлия Яковлева, ведущий эксперт цеха сортировки и комплектации алмазного сырья, автор предложения «Отказ от выходного контроля промпродукта после механизированной сортировки»:
— ?сходное сырье сортируется по цвету, форме и качеству на автоматах. Затем формируются готовые укрупненные позиции в соответствии с техническими требованиями к каждой размерности. ? остается промпродукт — это алмазы, которые сложно определить автоматам. А глаз специалиста справляется с этой задачей. Раньше ведущие эксперты в обязательном порядке делали анализ промпродукта. Это было нужно на начальном этапе работ по развитию механизированной сортировки для накопления статистики по алмазам, которые автоматы плохо идентифицируют.
Но поскольку эти алмазы затем все равно отправлялись на ручную пересортировку, я предложила исключить этап анализа промпродукта после автоматической сортировки и сразу после нее отправлять переходные алмазы на ручную сортировку.
Это позволило сократить время выходного анализа с участка механизированной сортировки, тем самым уменьшив трудозатраты на сортировку партии. Благодаря этой инициативе объем незавершенного производства сократился на $91 тыс.
Юлия Яковлева, ведущий эксперт цеха сортировки и комплектации алмазного сырья, автор предложения «Отказ от выходного контроля промпродукта после механизированной сортировки»:
— ?сходное сырье сортируется по цвету, форме и качеству на автоматах. Затем формируются готовые укрупненные позиции в соответствии с техническими требованиями к каждой размерности. ? остается промпродукт — это алмазы, которые сложно определить автоматам. А глаз специалиста справляется с этой задачей. Раньше ведущие эксперты в обязательном порядке делали анализ промпродукта. Это было нужно на начальном этапе работ по развитию механизированной сортировки для накопления статистики по алмазам, которые автоматы плохо идентифицируют.
Но поскольку эти алмазы затем все равно отправлялись на ручную пересортировку, я предложила исключить этап анализа промпродукта после автоматической сортировки и сразу после нее отправлять переходные алмазы на ручную сортировку.
Это позволило сократить время выходного анализа с участка механизированной сортировки, тем самым уменьшив трудозатраты на сортировку партии. Благодаря этой инициативе объем незавершенного производства сократился на $91 тыс.
#116
Отправлено 23 April 2020 - 11:56 AM
АЛРОСА Как сократить сроки подписания контрактов
Виктория Козлова, ведущий специалист отдела сопровождения продаж, автор предложения «Согласование и подписание контрактов отделом сопровождения продаж»:
— Мы пытались решить проблему больших затрат времени и сил на согласование и подписание контрактов, а также минимизировать риски, связанные с невозможностью проверить подлинность подписи контрагента на контракте, риск утраты оригиналов контрактов в процессе пересылки. Предложение в итоге превратилось в проект из двух частей: оптимизация согласования и оптимизация подписания договоров.
Евгений Слепенко, начальник отдела сопровождения продаж:
— Процесс согласования представлял собой архаичный способ физического перемещения документов от одного согласующего к другому. По самым скромным подсчетам, только на хождение сотрудников из кабинета в кабинет затрачивается 5 полноценных рабочих дней в год! Мы внедрили согласование контрактов через Docs Vision, обеспечив защиту информации и продумав удобство хранения и поиска документов. Электронный формат согласования позволил сэкономить время сотрудников, сократить расходы на бумагу и время согласования. Следующим шагом станет сокращение списка согласующих и форм контракта. Сегодня список согласующих предусматривает участие всех заинтересованных подразделений. Однако 90% всех контрактов содержат стандартные условия. Логично единожды согласовать шаблон контракта со всеми необходимыми службами, а каждый такой типовой договор пускать на согласование по сокращенному маршруту.
Так появилось решение разделить контракты на типовые и нетиповые. Если контракт типовой, он будет согласовываться по короткому маршруту (3 участника); если в нем присутствуют эксклюзивные условия, он будет проходить маршрут полного согласования (7 участников). Контракт разбили на две части: общие условия, одинаковые для всех, по-другому — оферта (она будет опубликована на сайте компании), и индивидуальные условия, отражающие стоимость, состав сырья, адрес доставки и т. п. Подписание будет проводиться только для индивидуальной части контракта. Сейчас мы уже на финишной прямой по внедрению этого новшества.
Вторым этапом реализации проекта станет подписание контрактов с помощью электронной цифровой подписи (ЭЦП). Сейчас мы хотим провести тестовое подписание контрактов с участниками внутреннего рынка — наши клиенты с энтузиазмом восприняли идею, поскольку это ускорит процесс получения сырья.
Виктория Козлова, ведущий специалист отдела сопровождения продаж, автор предложения «Согласование и подписание контрактов отделом сопровождения продаж»:
— Мы пытались решить проблему больших затрат времени и сил на согласование и подписание контрактов, а также минимизировать риски, связанные с невозможностью проверить подлинность подписи контрагента на контракте, риск утраты оригиналов контрактов в процессе пересылки. Предложение в итоге превратилось в проект из двух частей: оптимизация согласования и оптимизация подписания договоров.
Евгений Слепенко, начальник отдела сопровождения продаж:
— Процесс согласования представлял собой архаичный способ физического перемещения документов от одного согласующего к другому. По самым скромным подсчетам, только на хождение сотрудников из кабинета в кабинет затрачивается 5 полноценных рабочих дней в год! Мы внедрили согласование контрактов через Docs Vision, обеспечив защиту информации и продумав удобство хранения и поиска документов. Электронный формат согласования позволил сэкономить время сотрудников, сократить расходы на бумагу и время согласования. Следующим шагом станет сокращение списка согласующих и форм контракта. Сегодня список согласующих предусматривает участие всех заинтересованных подразделений. Однако 90% всех контрактов содержат стандартные условия. Логично единожды согласовать шаблон контракта со всеми необходимыми службами, а каждый такой типовой договор пускать на согласование по сокращенному маршруту.
Так появилось решение разделить контракты на типовые и нетиповые. Если контракт типовой, он будет согласовываться по короткому маршруту (3 участника); если в нем присутствуют эксклюзивные условия, он будет проходить маршрут полного согласования (7 участников). Контракт разбили на две части: общие условия, одинаковые для всех, по-другому — оферта (она будет опубликована на сайте компании), и индивидуальные условия, отражающие стоимость, состав сырья, адрес доставки и т. п. Подписание будет проводиться только для индивидуальной части контракта. Сейчас мы уже на финишной прямой по внедрению этого новшества.
Вторым этапом реализации проекта станет подписание контрактов с помощью электронной цифровой подписи (ЭЦП). Сейчас мы хотим провести тестовое подписание контрактов с участниками внутреннего рынка — наши клиенты с энтузиазмом восприняли идею, поскольку это ускорит процесс получения сырья.
#117
Отправлено 24 April 2020 - 11:05 AM
Тихвинский вагоностроительный завод (ТВСЗ):
Внедрение кайдзен-предложения в производство зачастую позволяет не только сократить временные затраты или улучшить эргономичность рабочего места, но и значительно сэкономить. Пример рационального подхода к своей работе продемонстрировал начальник участка ремонта оборудования производства крышек люка и обработки высокопрочного чугуна ТВСЗ Алексей Заболотских. В процессе эксплуатации закалочной печи «JLBECKER», в которой производится температурная обработка ряда деталей для вагонной тележки - круглого корпуса, круглого колпака и клиньев, произошла поломка. В конструкции прогорело защитное одеяло, а именно, дорогостоящая керамическая плита. На замену потребовалась бы не одна сотня тысяч рублей, кроме того, это было чревато длительным простоем производства.
- Проанализировав всевозможные типы материалов и проведя ряд экспериментов, было принято решение установить пластины из жаропрочной стали, которые выдерживают аналогичную нагрузку и могут работать в заданной температурной среде, которая имеется в печи, - рассказал Алексей Заболотских.
Внедрение рационализаторской идеи Алексея позволило значительно сократить затраты предприятия и не допустить остановки производства высокопрочных деталей. Пластины, вмонтированные в конструкцию печи, прекрасно себя зарекомендовали и по мнению автора могут функционировать без замены в течение 6 месяцев.
Внедрение кайдзен-предложения в производство зачастую позволяет не только сократить временные затраты или улучшить эргономичность рабочего места, но и значительно сэкономить. Пример рационального подхода к своей работе продемонстрировал начальник участка ремонта оборудования производства крышек люка и обработки высокопрочного чугуна ТВСЗ Алексей Заболотских. В процессе эксплуатации закалочной печи «JLBECKER», в которой производится температурная обработка ряда деталей для вагонной тележки - круглого корпуса, круглого колпака и клиньев, произошла поломка. В конструкции прогорело защитное одеяло, а именно, дорогостоящая керамическая плита. На замену потребовалась бы не одна сотня тысяч рублей, кроме того, это было чревато длительным простоем производства.
- Проанализировав всевозможные типы материалов и проведя ряд экспериментов, было принято решение установить пластины из жаропрочной стали, которые выдерживают аналогичную нагрузку и могут работать в заданной температурной среде, которая имеется в печи, - рассказал Алексей Заболотских.
Внедрение рационализаторской идеи Алексея позволило значительно сократить затраты предприятия и не допустить остановки производства высокопрочных деталей. Пластины, вмонтированные в конструкцию печи, прекрасно себя зарекомендовали и по мнению автора могут функционировать без замены в течение 6 месяцев.
#118
Отправлено 08 May 2020 - 01:15 PM
Как на ОЭМК усовершенствовали автошлаковозы
В автотранспортном цехе Оскольского электрометаллургического комбината (компания «Металлоинвест») провели модернизацию двух атошлаковозов, заменив пневматическую систему управления двигателем на гидравлику.
Это привело к сокращению удельного расхода топлива, а также позволило исключить закупку дорогостоящих деталей для ремонта технологического транспорта и сделать управление автошлаковозом более точным и надёжным.
«Старая пневматическая система подачи топлива работала за счет компрессоров, фильтросушителей, ремней и других деталей, которые периодически выходили из строя, - рассказывает автор идеи, мастер по ремонту транспорта автотранспортного цеха ОЭМК Александр Карапузов. – А так как у шлаковозов довольно интенсивная работа и большая нагрузка, то, к примеру, ремни выдерживали всего две-три смены.
Свое рацпредложение Александр Карапузов реализовал вместе с коллегами в начале апреля, и оно уже показало эффективность. С автошлаковоза была полностью удалена пневматическая система, которая обеспечивала управление не только топливным насосом, но и защитными жалюзи, и установлена гидравлическая система.
Теперь жалюзи, закрывающие окна шлаковоза от попадания шлака, также управляются с помощью гидравлического привода, и благодаря этому сокращается удельный расход топлива. Кроме того, новые двигатели в отличие от «родных», стоявших на автошлаковозах, прекрасно работают без компрессоров, а значит, теперь нет необходимости в закупке дорогостоящих механизмов. А главное – эту систему можно успешно применять и на некотором другом технологическом транспорте, что принесет автоцеху и комбинату определённый экономический эффект.
В автотранспортном цехе Оскольского электрометаллургического комбината (компания «Металлоинвест») провели модернизацию двух атошлаковозов, заменив пневматическую систему управления двигателем на гидравлику.
Это привело к сокращению удельного расхода топлива, а также позволило исключить закупку дорогостоящих деталей для ремонта технологического транспорта и сделать управление автошлаковозом более точным и надёжным.
«Старая пневматическая система подачи топлива работала за счет компрессоров, фильтросушителей, ремней и других деталей, которые периодически выходили из строя, - рассказывает автор идеи, мастер по ремонту транспорта автотранспортного цеха ОЭМК Александр Карапузов. – А так как у шлаковозов довольно интенсивная работа и большая нагрузка, то, к примеру, ремни выдерживали всего две-три смены.
Свое рацпредложение Александр Карапузов реализовал вместе с коллегами в начале апреля, и оно уже показало эффективность. С автошлаковоза была полностью удалена пневматическая система, которая обеспечивала управление не только топливным насосом, но и защитными жалюзи, и установлена гидравлическая система.
Теперь жалюзи, закрывающие окна шлаковоза от попадания шлака, также управляются с помощью гидравлического привода, и благодаря этому сокращается удельный расход топлива. Кроме того, новые двигатели в отличие от «родных», стоявших на автошлаковозах, прекрасно работают без компрессоров, а значит, теперь нет необходимости в закупке дорогостоящих механизмов. А главное – эту систему можно успешно применять и на некотором другом технологическом транспорте, что принесет автоцеху и комбинату определённый экономический эффект.
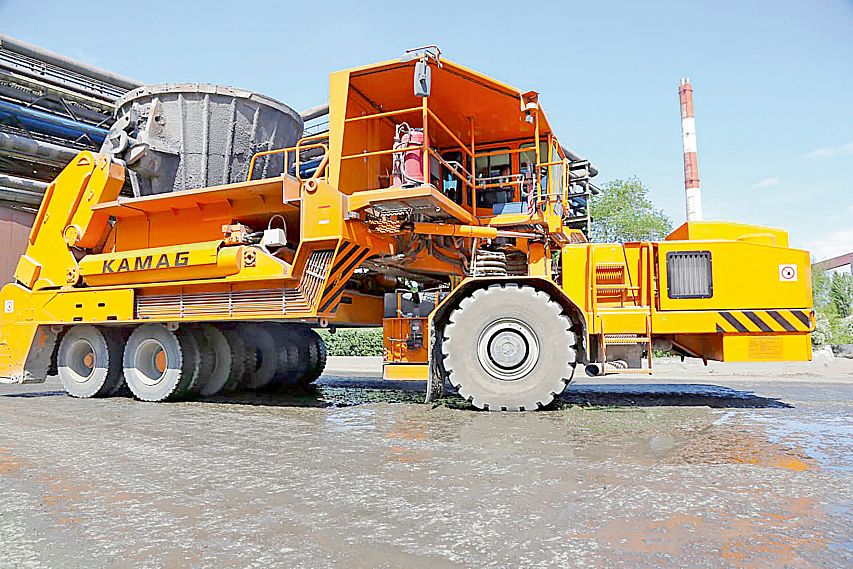
#119
Отправлено 13 May 2020 - 01:43 PM
Кайдзен «Увеличение ходимости форсуночного узла» в отделении № 6 «Порошковой металлургии Волгоград» (ПМВ)
Раньше для подготовки к работе форсуночный узел разогревали до 650 °С, что часто приводило к нарушению его геометрии, вследствие чего он мог работать нестабильно, а его ходимость – непрерывная работа – составляла не более 5 часов 20 минут.
Для решения этой проблемы мастер отделения № 6 Денис Бездняк предложил разогревать не весь узел, а только его металлопровод – чугунное колено. Для реализации его задумки работники предприятия вначале изучили температурный режим работы узла, а затем попробовали нагреть колено узла природным газом, но желаемого результата это не принесло. Со временем металлурги решили кардинально поменять подход и изготовили специальную шторку со вставкой для разогрева колена.
– Приспособив шторку на боковом окне пульверизационной установки, нам удалось разогреть металлопровод форсунки до нужной температуры, не перегревая корпус самой форсунки, – рассказывает начальник ОРПС Анатолий Барсуков. – В результате он перестал деформироваться, но при этом сохранялись требуемые вакуумные характеристики, а ходимость форсуночного узла выросла до 7 часов.
После реализации этого улучшения работникам ПМВ удалось снизить затраты до 30% на закупку новых форсунок и комплектующих для их ремонта.
Для дальнейшего повышения экономической эффективности директор по производству Александр Торопов и старший мастер отделения № 6 Александр Сухенко предложили заменить материал форсунки с нержавейки на обычную сталь, тем самым снизив стоимость одной форсунки на 10%. А чтобы отслеживать правильность разогрева корпуса форсунки, работники предприятия применили простое, но в то же время эффективное решение – закрепили на ее корпусе специальную алюминиевую бирку с номером форсунки. Теперь если плавильщик неправильно разогреет форсунку, алюминиевая бирка расплавится.
Текст: Виталий АНДРОСОВ
Благодарим редакцию газеты "Вестник РУСАЛа" за предоставление данного материала.
Раньше для подготовки к работе форсуночный узел разогревали до 650 °С, что часто приводило к нарушению его геометрии, вследствие чего он мог работать нестабильно, а его ходимость – непрерывная работа – составляла не более 5 часов 20 минут.
Для решения этой проблемы мастер отделения № 6 Денис Бездняк предложил разогревать не весь узел, а только его металлопровод – чугунное колено. Для реализации его задумки работники предприятия вначале изучили температурный режим работы узла, а затем попробовали нагреть колено узла природным газом, но желаемого результата это не принесло. Со временем металлурги решили кардинально поменять подход и изготовили специальную шторку со вставкой для разогрева колена.
– Приспособив шторку на боковом окне пульверизационной установки, нам удалось разогреть металлопровод форсунки до нужной температуры, не перегревая корпус самой форсунки, – рассказывает начальник ОРПС Анатолий Барсуков. – В результате он перестал деформироваться, но при этом сохранялись требуемые вакуумные характеристики, а ходимость форсуночного узла выросла до 7 часов.
После реализации этого улучшения работникам ПМВ удалось снизить затраты до 30% на закупку новых форсунок и комплектующих для их ремонта.
Для дальнейшего повышения экономической эффективности директор по производству Александр Торопов и старший мастер отделения № 6 Александр Сухенко предложили заменить материал форсунки с нержавейки на обычную сталь, тем самым снизив стоимость одной форсунки на 10%. А чтобы отслеживать правильность разогрева корпуса форсунки, работники предприятия применили простое, но в то же время эффективное решение – закрепили на ее корпусе специальную алюминиевую бирку с номером форсунки. Теперь если плавильщик неправильно разогреет форсунку, алюминиевая бирка расплавится.
Текст: Виталий АНДРОСОВ
Благодарим редакцию газеты "Вестник РУСАЛа" за предоставление данного материала.
#120
Отправлено 15 May 2020 - 01:30 PM
Как улучшить работу автослесарей - опыт транспортного управления АО «Уралэлектромедь»
Автор идеи - Андрей Раев, слесарь по ремонту транспортных средств:
— В процессе внедрения системы 5S я проанализировал работу автослесарей и задумался: а так ли удобно расположены верстаки во втором и третьем ремонтных боксах ПТС АТЦ? ? предложил оборудовать слесарный верстак поворотными колесами и немного укоротить его, предварительно снизив центр тяжести. Я рассчитал, что так верстак будет более мобильным и перестанет загромождать ремонтный бокс. Как следствие, сократится и время на подготовку к ремонту. К верстаку с торцов приварил ручки для удобного его перемещения и два лотка под чистую ветошь и б/у материалы, закрепил стойку для крепления переноски.
В ходе испытаний предложение Андрея Раева принесло экономический эффект в размере 106,8 тыс. рублей, в цехе принято решение изготовить 10 таких мобильных рабочих мест на участках с большой площадью перемещения.
Автор идеи - Андрей Раев, слесарь по ремонту транспортных средств:
— В процессе внедрения системы 5S я проанализировал работу автослесарей и задумался: а так ли удобно расположены верстаки во втором и третьем ремонтных боксах ПТС АТЦ? ? предложил оборудовать слесарный верстак поворотными колесами и немного укоротить его, предварительно снизив центр тяжести. Я рассчитал, что так верстак будет более мобильным и перестанет загромождать ремонтный бокс. Как следствие, сократится и время на подготовку к ремонту. К верстаку с торцов приварил ручки для удобного его перемещения и два лотка под чистую ветошь и б/у материалы, закрепил стойку для крепления переноски.
В ходе испытаний предложение Андрея Раева принесло экономический эффект в размере 106,8 тыс. рублей, в цехе принято решение изготовить 10 таких мобильных рабочих мест на участках с большой площадью перемещения.
1 человек читают эту тему
0 пользователей, 1 гостей, 0 скрытых пользователей