Добро пожаловать в Сообщество производственных менеджеров
![]() |
Добро пожаловать в Сообщество производственных менеджеров, промышленный форум номер один в России и СНГ. Регистрация открыта для всех, поэтому зарегистрируйтесь и принимайте участие в дискуссиях прямо сейчас! Вход Регистрация |

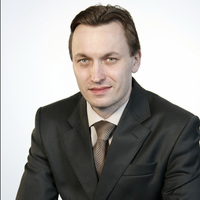
Бережливое производство в многономенклатурном производстве
Автор: Илья Паутов, ноя 11 2013 04:57
10 сообщений в этой теме
#1
Отправлено 11 Ноябрь 2013 - 04:57
Коллеги, очень сильно хочется узнать про положительные практики развертывания бережливого производства и применения конкретных инструментов в многономенклатурном производстве.
Когда производственное подразделение производит в месяц 2, 10 или 20 номенклатурных позиций, то здесь все понятно и просто, а вот когда в месяц необходимо производить от 2500 до 5000 различных номенклатурных позиций, то вот здесь возникают проблемы, связанные с применением инструментов бережливого производства, а также с выстраиванием потоков.
Вообщем, когда мало, то все понятно, а когда много, то, честно, не совсем понятно, что делать.
Если у кого-то есть положительные примеры бережливого производства в многонаменлатурном производстве, то расскажите о них, пожалуйста, а лучше покажите. Буду очень благодарен.
Когда производственное подразделение производит в месяц 2, 10 или 20 номенклатурных позиций, то здесь все понятно и просто, а вот когда в месяц необходимо производить от 2500 до 5000 различных номенклатурных позиций, то вот здесь возникают проблемы, связанные с применением инструментов бережливого производства, а также с выстраиванием потоков.
Вообщем, когда мало, то все понятно, а когда много, то, честно, не совсем понятно, что делать.
Если у кого-то есть положительные примеры бережливого производства в многонаменлатурном производстве, то расскажите о них, пожалуйста, а лучше покажите. Буду очень благодарен.
#2
Отправлено 11 Ноябрь 2013 - 09:04
Как раз наш случай, примерно 5 000 - 7 000 позиций ежемесячно. Самое понятное решение - уменьшать минимально возможный размер партии, выстраивать короткие потоки и отделять их друг от друга супермаркетами. Сложно, но по-другому ничего не получается.
#3
Отправлено 18 Ноябрь 2013 - 10:33
Вопрос очень интересный. Действительно, практика внедрения бережливого производства хорошо описывается применительно к автомобильной промышленности. Говорить о таких понятиях как такт, когда номенклатура деталей в цехе несколько тысяч, а партия обработки одной детали несколько штук, согласитесь, трудно. При этом все детали разные.
У нас как раз такое производство. Самая большая проблема – это потери связанные с переналадкой оборудования. Конечно, можно обрабатывать оптимальные партии, но при этом растут запасы. Поэтому мы пошли другим путем, а именно сокращением потерь при переналадке. У нас есть нормативы переналадки, матрицы переналадки. Достаточно сказать, что время переналадки токарного обрабатывающего центра WFL-35 (Австрия) или ИНТЕГРЕКС 300 СТ (Япония) занимает не более 30 минут. Приезжайте, покажем. Номенклатура станков, прессов очень большая и эти приемы внедрены везде. Это был целый проект, а занимались этой работой с 2005 года. Начинали с двух смен, а довели до 30 минут. Причем, детали сложные. Ну о других инструментах расскажу в другой раз.
У нас как раз такое производство. Самая большая проблема – это потери связанные с переналадкой оборудования. Конечно, можно обрабатывать оптимальные партии, но при этом растут запасы. Поэтому мы пошли другим путем, а именно сокращением потерь при переналадке. У нас есть нормативы переналадки, матрицы переналадки. Достаточно сказать, что время переналадки токарного обрабатывающего центра WFL-35 (Австрия) или ИНТЕГРЕКС 300 СТ (Япония) занимает не более 30 минут. Приезжайте, покажем. Номенклатура станков, прессов очень большая и эти приемы внедрены везде. Это был целый проект, а занимались этой работой с 2005 года. Начинали с двух смен, а довели до 30 минут. Причем, детали сложные. Ну о других инструментах расскажу в другой раз.
#4
Отправлено 19 Ноябрь 2013 - 08:56
Да, единственно верный путь - повышение эффективности переналадки. Очень хорошо об этом пишут в методической литературе по SMED, хотя за всем стоИт обычная логика: разделить операции по переналадке на внешние и внутренние, и максимально вынести внешние за рамки времени остановки машины. Увеличивать размер партий никак нельзя, т.к. это приведет к излишним запасам и к неэффективному использованию капитала.
#5
Отправлено 19 Ноябрь 2013 - 10:29
Да, конечно, быстрая переналадка важна, но, на мой взгляд, это не путь, это инструмент - она позволяет сократить размер оптимальной партии, как следствие - оперативно управлять запасами и в итоге сократить время исполнения заказа. Кроме того, чем меньше партия, тем проще выявлять отклонения по качеству и количеству. А путь - это так или иначе вытягивающий поток.
Я предложил бы сначала стабилизировать процесс, выстроить поток и задать ритм его работы (даже если сложно определить время такта). После этого можно делать все остальное: управлять запасами, оптимизировать логистику, встраивать качество, сокращать время, укорачивать и расширять поток, изменять оргструктуру и т.д. В качестве регуляторов потока очень хороший результат дают супермаркеты, для прямого сокращения времени исполнения заказа часто полезны производственные ячейки и управление инструментом и оснасткой.
Я предложил бы сначала стабилизировать процесс, выстроить поток и задать ритм его работы (даже если сложно определить время такта). После этого можно делать все остальное: управлять запасами, оптимизировать логистику, встраивать качество, сокращать время, укорачивать и расширять поток, изменять оргструктуру и т.д. В качестве регуляторов потока очень хороший результат дают супермаркеты, для прямого сокращения времени исполнения заказа часто полезны производственные ячейки и управление инструментом и оснасткой.
#6
Отправлено 20 Ноябрь 2013 - 08:45
Ответ пришел по почте:
"В конкретном вопросе о многономенклатурном производстве у меня было много «опытов», расскажу об одном, недавнем:
С целью снижения НЗП на предприятии стояла задача выстраивания потоков единичных изделий, начали с участка сборки – там получилась и работа по Тт и снижение НЗП и увеличение скорости прохождения изделий и т.д. Придя на участки механообработки (номенклатура 500), и приняв концепцию перехода от, так называемого «квадратно-гнездового» метода производства (когда участки выстраиваются по методу обработки) к «потоковому», мы столкнулись с конкретными проблемами, рассказываю на примере. Выстроив поток единичных изделий в ячейке из 4 рабочих мест (оборудование) по одному из комплектующих изделий мы поняли, что загрузка оборудования при этом будет «ниже плинтуса», об эффективности при этом можно забыть, это отразится на себестоимости. От концепции отходить не хотелось, поэтому начали искать другие решения. Нашли. Казалось безумное предложение по введению в эту ячейку еще 7! (для полной загрузки оборудования) номенклатур с похожими, но не копирующими тех.операциями и последовательностью изготовления. Процесс доведения до «идеала» (идеала не существует и процесс до сих пор улучшают, но немного медленнее) ячейки занял 6,5 месяцев ежедневной кропотливой работы группы во главе с бригадиром (ЛМГ) + технолог + специалист ПС принесли следующие результаты: в ячейке стали изготавливаться 8 номенклатур изделий на 6 ед. оборудования(раб. местах), ПЕИ получился только на 3 изделиях остальные изготавливаются с разной партийностью от 3 до 10 единиц. В целом, НЗП на этих потоках снизилось на 93%! Ну и естественно значительно улучшились все сопутствующие показатели себестоимости: производительность, качество, логистика, и т.д.
Пытаюсь донести подробно это для того, чтобы было понятно, что многономенклатурность всегда плохо для производства, но бывает, что этим решаются другие проблемы, и здесь уже приходится считать, ЧТО ВЫГОДНЕЕ.
Я считаю, что есть только один путь развития – это увидеть (понять) проблему, проанализировать, наметить пути ее решения, провести МЛН. экспериментов и придти к взаимовыгодному решению. В этой формуле ничего нового нет, все дело в действии. А какое д.б. действие – в каждом конкретном случае свое, и этому не научишь, просто надо идти и действовать. Вот такая простая формула."
"В конкретном вопросе о многономенклатурном производстве у меня было много «опытов», расскажу об одном, недавнем:
С целью снижения НЗП на предприятии стояла задача выстраивания потоков единичных изделий, начали с участка сборки – там получилась и работа по Тт и снижение НЗП и увеличение скорости прохождения изделий и т.д. Придя на участки механообработки (номенклатура 500), и приняв концепцию перехода от, так называемого «квадратно-гнездового» метода производства (когда участки выстраиваются по методу обработки) к «потоковому», мы столкнулись с конкретными проблемами, рассказываю на примере. Выстроив поток единичных изделий в ячейке из 4 рабочих мест (оборудование) по одному из комплектующих изделий мы поняли, что загрузка оборудования при этом будет «ниже плинтуса», об эффективности при этом можно забыть, это отразится на себестоимости. От концепции отходить не хотелось, поэтому начали искать другие решения. Нашли. Казалось безумное предложение по введению в эту ячейку еще 7! (для полной загрузки оборудования) номенклатур с похожими, но не копирующими тех.операциями и последовательностью изготовления. Процесс доведения до «идеала» (идеала не существует и процесс до сих пор улучшают, но немного медленнее) ячейки занял 6,5 месяцев ежедневной кропотливой работы группы во главе с бригадиром (ЛМГ) + технолог + специалист ПС принесли следующие результаты: в ячейке стали изготавливаться 8 номенклатур изделий на 6 ед. оборудования(раб. местах), ПЕИ получился только на 3 изделиях остальные изготавливаются с разной партийностью от 3 до 10 единиц. В целом, НЗП на этих потоках снизилось на 93%! Ну и естественно значительно улучшились все сопутствующие показатели себестоимости: производительность, качество, логистика, и т.д.
Пытаюсь донести подробно это для того, чтобы было понятно, что многономенклатурность всегда плохо для производства, но бывает, что этим решаются другие проблемы, и здесь уже приходится считать, ЧТО ВЫГОДНЕЕ.
Я считаю, что есть только один путь развития – это увидеть (понять) проблему, проанализировать, наметить пути ее решения, провести МЛН. экспериментов и придти к взаимовыгодному решению. В этой формуле ничего нового нет, все дело в действии. А какое д.б. действие – в каждом конкретном случае свое, и этому не научишь, просто надо идти и действовать. Вот такая простая формула."
#7
Отправлено 20 Ноябрь 2013 - 11:34
Здесь необходимо шлифовать SMED (быстрая переналадка) и TPS (всеобщее обслуживание оборудования). Разумеется нельзя забывать о 5с, стандартизации и др.
#8
Отправлено 22 Ноябрь 2013 - 03:36
Илья, приветствую!
ПС предприятия не равно "инструментарию Lean"!
Что Вы можете сделать в многономенклатурном производстве с использованием инструментов Lean - это "заставить"/помочь производство работать "быстрее". Начав с разделения (физического или логического) потоков деталей (групп) деталей, жесткого закрепления деталей за станками (это в любом случае надо делать обязательно!), далее - 5С, визуализация и стандартизация (не повредит). И только после этого, и только если надо (надо смотреть статистику по ОЕЕ по участкам/группам оборудования) - многими здесь любимый но не всегда нужный SMED. По поводу советов единичного потока - конечно это классно, производить "штучно", кто спорит, но не для большинства ваших переделов (штучное лопаточное производство - будет интересно посмотреть...).
Что Вы этим (см. выше) добьетесь: ваше производство будет довольно эффективно производить "штуки". И все.. Но - и это самое важное, т.к. и есть цель внедрения Lean (о чем либо забывают, либо просто не знают...) - Вам надо, чтобы ваше производство эффективно - т.е. "Точно Вовремя" - производило только нужные клиенту или следующему потребителю ("поставщику") "штуки", а не просто эффективно и "бережливо" плодило никому ненужную незавершенку!
А для этого вам надо ставить систему планирования, т..е. систему управления информационными потоками. А это - не модная, не простая и абсолютно не "бережливая" хотя и Lean штука...
Для штучного, квази-серийного производства, и/или небольших по длительности переделов, и/или под фиксированный и неизменный такт сборки (конвейера) ПС = вытягивание через канбан или супермаркет. Для Вашего случая производства ГТД "от руды", когда "внешний" (для "деталеделательного" многономенклатурного производства) нестабильный, детали под разные "темы" постоянно пересекаются, сроки сборки (из-за объективных и субъективных причин) - постоянно меняются - канбан/супермаркет в чистом виде - путь в никуда. Необходимо ставить систему "вытягивающего" под сборку планирования, с жестким или мягким "распределением" под сборку и запасов на производственных складах и запасов НзП (т.е. уже запущенных производственных заданий/партий) и, обязательно с ограничивающим (у вас же "сделка"?) и приоритезированным управлением запуском, которое, в вашем случае, лучше всего организовать с помощью вытягивающе-проталкивающей системы: генерация электронного канбан под сборку (под последовательность сбокри), который будет выступать заданием на запуск производства с "начинающих" переделов. Это может быть и литье, но скорее всего - нет, скорее всего начинать надо с мехобработки. При этом, управление квази-стабильными потоками ДСЕ (возможно, что это некоторые наименования/группы тех-же лопаток, другая "массовая" механика и/или нормали) можно и нужно делать с использованием локального ("внутрицеха" - "связка двух (поставщик-потребитель) цехов") вытягивания (супермаркеты на механосборке/сборке) .
И, естественно, в ваших условиях (SaM 146 + ГТД и наземные и нет, спецтематика и пр...) - без "правильной", Lean, в хорошем смысле слова, информационной системы планирования и управления производством Вам не обойтись.
Не надо применять "БП" там, где его не надо и бесполезно применять.
Если интересует больше конкретики по практической реализации - задавайте вопросы, хотя описание такой ПС - дело немаленькой статьи; частично есть здесь http://www.up-pro.ru...nie-rodova.html - вам (Сатурну), для квази-серийного производства многое хорошо подойдет.
ПС предприятия не равно "инструментарию Lean"!
Что Вы можете сделать в многономенклатурном производстве с использованием инструментов Lean - это "заставить"/помочь производство работать "быстрее". Начав с разделения (физического или логического) потоков деталей (групп) деталей, жесткого закрепления деталей за станками (это в любом случае надо делать обязательно!), далее - 5С, визуализация и стандартизация (не повредит). И только после этого, и только если надо (надо смотреть статистику по ОЕЕ по участкам/группам оборудования) - многими здесь любимый но не всегда нужный SMED. По поводу советов единичного потока - конечно это классно, производить "штучно", кто спорит, но не для большинства ваших переделов (штучное лопаточное производство - будет интересно посмотреть...).
Что Вы этим (см. выше) добьетесь: ваше производство будет довольно эффективно производить "штуки". И все.. Но - и это самое важное, т.к. и есть цель внедрения Lean (о чем либо забывают, либо просто не знают...) - Вам надо, чтобы ваше производство эффективно - т.е. "Точно Вовремя" - производило только нужные клиенту или следующему потребителю ("поставщику") "штуки", а не просто эффективно и "бережливо" плодило никому ненужную незавершенку!
А для этого вам надо ставить систему планирования, т..е. систему управления информационными потоками. А это - не модная, не простая и абсолютно не "бережливая" хотя и Lean штука...
Для штучного, квази-серийного производства, и/или небольших по длительности переделов, и/или под фиксированный и неизменный такт сборки (конвейера) ПС = вытягивание через канбан или супермаркет. Для Вашего случая производства ГТД "от руды", когда "внешний" (для "деталеделательного" многономенклатурного производства) нестабильный, детали под разные "темы" постоянно пересекаются, сроки сборки (из-за объективных и субъективных причин) - постоянно меняются - канбан/супермаркет в чистом виде - путь в никуда. Необходимо ставить систему "вытягивающего" под сборку планирования, с жестким или мягким "распределением" под сборку и запасов на производственных складах и запасов НзП (т.е. уже запущенных производственных заданий/партий) и, обязательно с ограничивающим (у вас же "сделка"?) и приоритезированным управлением запуском, которое, в вашем случае, лучше всего организовать с помощью вытягивающе-проталкивающей системы: генерация электронного канбан под сборку (под последовательность сбокри), который будет выступать заданием на запуск производства с "начинающих" переделов. Это может быть и литье, но скорее всего - нет, скорее всего начинать надо с мехобработки. При этом, управление квази-стабильными потоками ДСЕ (возможно, что это некоторые наименования/группы тех-же лопаток, другая "массовая" механика и/или нормали) можно и нужно делать с использованием локального ("внутрицеха" - "связка двух (поставщик-потребитель) цехов") вытягивания (супермаркеты на механосборке/сборке) .
И, естественно, в ваших условиях (SaM 146 + ГТД и наземные и нет, спецтематика и пр...) - без "правильной", Lean, в хорошем смысле слова, информационной системы планирования и управления производством Вам не обойтись.
Не надо применять "БП" там, где его не надо и бесполезно применять.
Если интересует больше конкретики по практической реализации - задавайте вопросы, хотя описание такой ПС - дело немаленькой статьи; частично есть здесь http://www.up-pro.ru...nie-rodova.html - вам (Сатурну), для квази-серийного производства многое хорошо подойдет.
#9
Отправлено 03 Декабрь 2013 - 10:54
Ответ пришел по почте:
Все просто - либо Вы занимаетесь БП для повышения эффективности и сокращения потерь, либо ищете отговорки, почему этим заниматься не надо. Я скажу больше, если у Вас 5-10 наименований в номенклатуре, это значит, что Ваши изделия очень сложные длинноцикловые и вот именно там БП заниматься очень сложно. Если у Вас в номенклатуре 2500-5000 наименований, значит изделия очень простые с очень коротким циклом, вот простыми и короткоцикловыми деталями заниматься БП не сложно.
Все просто - либо Вы занимаетесь БП для повышения эффективности и сокращения потерь, либо ищете отговорки, почему этим заниматься не надо. Я скажу больше, если у Вас 5-10 наименований в номенклатуре, это значит, что Ваши изделия очень сложные длинноцикловые и вот именно там БП заниматься очень сложно. Если у Вас в номенклатуре 2500-5000 наименований, значит изделия очень простые с очень коротким циклом, вот простыми и короткоцикловыми деталями заниматься БП не сложно.
#10
Отправлено 05 Декабрь 2013 - 12:23
Считаю, количество номенклатурных позиций не играет никакой роли в применении бережливого производства. Система бережливого производства изучает любой процесс, устраняет потери, проводит изменения по улучшению. А грамотный индустриальный инженер скоординирует работу цеха с применением бережливого производства. Здесь, безусловно, будут свои особенности, но шаг за шагом, последовательно и целенаправленно, можно внедрять общие инструменты и принципы бережливого производства на любом производстве с любой номенклатурой.
1 человек читают эту тему
0 пользователей, 1 гостей, 0 скрытых пользователей